Laguna Clothing Private Limited - KPR unit
LEED V4.1 Platinum Rated Garment Factory
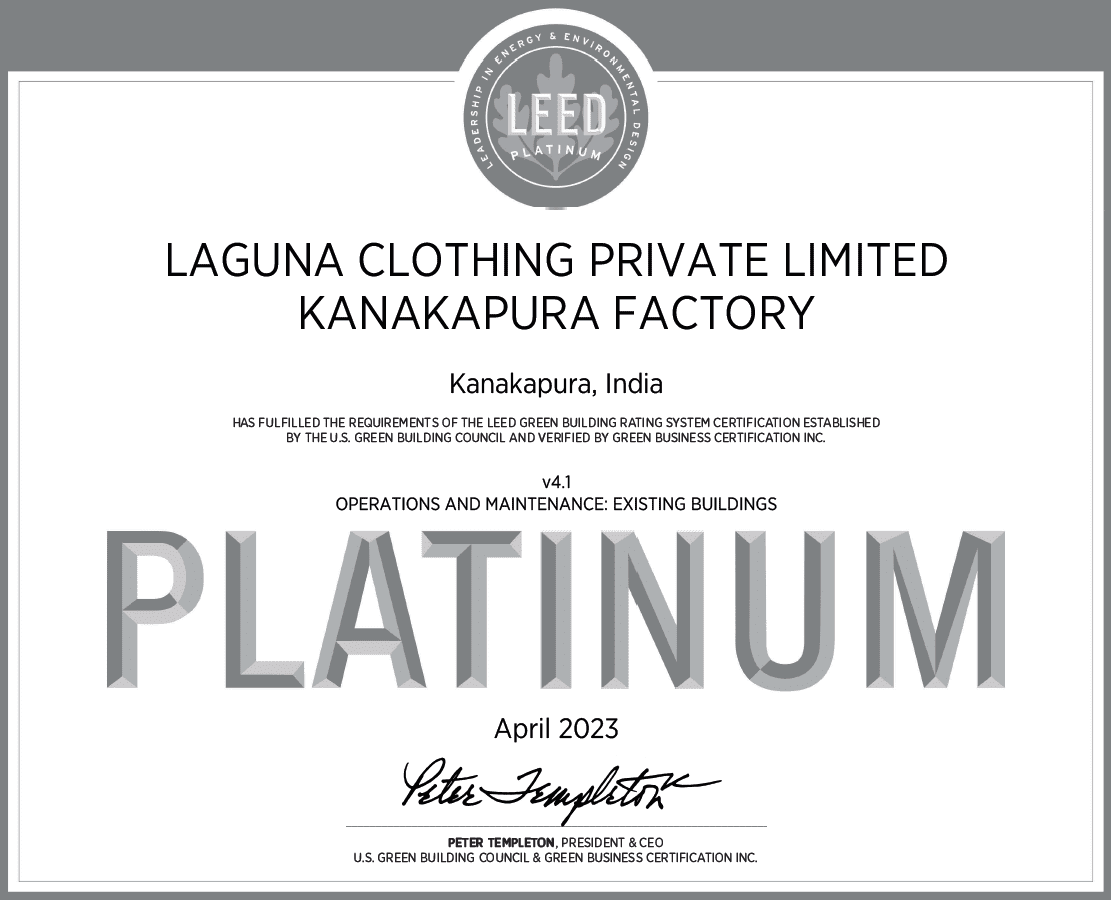
InHabit is proud to announce that Laguna Clothing - KPR Unit has been awarded the prestigious Platinum Rating in the LEED V4.1 Existing Buildings Operations and Maintenance Rating system
InHabit has provided green building consultation and ratings facilitation services to Laguna Clothing Private Limited for their KPR Unit Garment Factory at Kanakapura, Bengaluru, Karnataka.
The factory has exceeded Global and local averages in energy, waste, transportation and human experience criteria's.
Laguna has scored a phenomenal 84 points out of the available 100 points making it one of the greenest garment factories in the region.
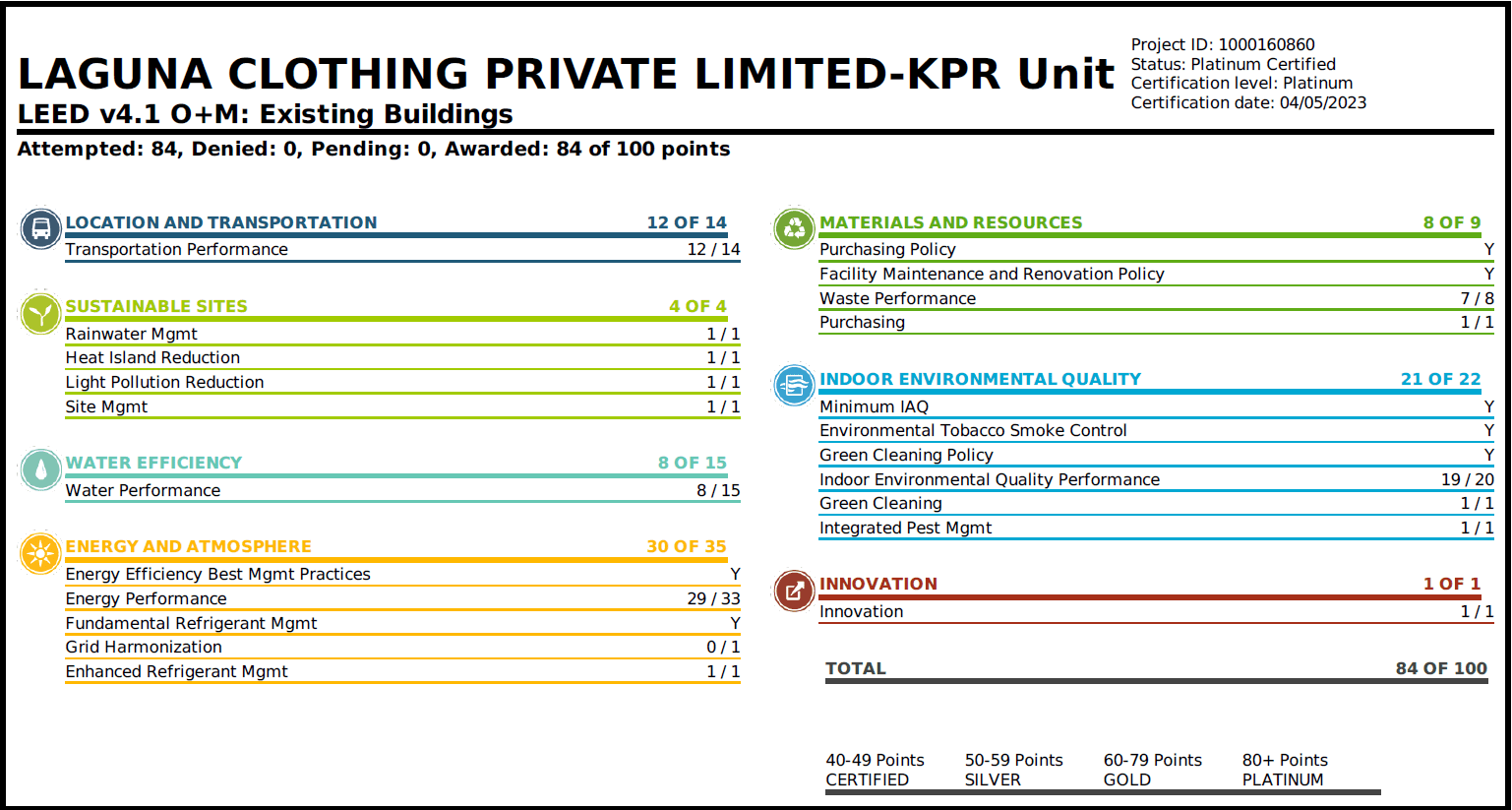
The development achieves 40% potable water savings compared to NBC standards by installing water efficient plumbing fixtures.
Large quantities of water is saved in irrigation by using the treated wastewater and stored rainwater to meet 100% of the irrigation demand..
100% wastewater is treated to tertiary standards and will be used for landscaping & flushing purposes.
The site is a zero-discharge site with 100% of rainwater is stored and reused with the excess being recharged.
Highly efficient drip and sprinkler irrigation systems are installed to further minimise non-potable water use.
Domestic Water quality is regularly tested to ensure all BIS norms are met.
All major sources of water consumption will be sub metered and monitored on a regular basis to identify any wastage.
All restrooms are being upgraded phase wise to incorporate waterless urinals.
- The project has 227 KW solar PV system installed on the roof which caters to most of the non-process loads and has helped reduce the building's energy consumption by over 40%.
- Energy meters have been installed in all major energy consuming areas including process loads and building loads.
- The entire factory, admin areas, conference room and other ancillary facilities are completely naturally ventilated and non air-conditioned and no air conditioning equipment is installed anywhere on the factory premises.
- An ASHRAE level 3 energy audit was conducted to identify all areas of energy usage and every energy efficiency measure recommended is actioned phase wise.
- All lighting has been upgraded to high LPD LEDs with daylight sensors incorporated for all daylit areas.
- Innovations have been done in the fusing machines with additional conveyors eliminating the need for at least one machine.
- One DG set has been decommissioned over time by improving the overall energy efficiency in the factory.
- Laguna Clothing LLP has some of the most prolific records in the textile industry for generating the least amount of waste per shirt with less than 0.5% landfill discharge.
- All procurements are done through a local grocery store which in turn procures the raw material from the Kanakapura Farmers markets.
- The project already has sustainable purchasing practices in place. These have now been formalised through the purchasing policy which has been created using the LEED V4.1 framework.
- A dedicated team and a waste storage space are provided to store the collected waste before handing it over to the third-party recycler. The collected waste which are generated such as Paper, Plastic, Cartons, Chindi will be sent to recycling on a weekly basis.
- All printing paper used at the factory is recycled paper only, additionally all IT equipment is energy star certified.
- The project is designed to ensure over 100% of the regularly occupied spaces have Fresh air ventilation.
- Over 60% of the Building Occupants has Connectivity to the Exterior View.
- All common areas in the building will be declared as no smoking zones.
- Periodic indoor air quality tests are done to keep a check on indoor environmental conditions and remedial measures are taken as per the pollutant identified.
- Annual human experience surveys are conducted among 25% of the staff to study the comfort conditions and record details of any workplace issues faced by the staff.
- The factory has fully changed over to organic pest management and organic landscaping practices to minimise the use of harmful chemicals in the factory.
- All food served at the factory procured within 150 Kms radius to ensure freshness and minimise its transportation impact.
- The factory follows a robust green cleaning policy and has fully upgraded to using only natural and organic green cleaners.