InHabit is proud to announce that the admin office of Mapal India Pvt Ltd has been awarded the prestigious Platinum rating in the USGBC LEED v4.1 Building Design + Construction green building rating system.
InHabit has provided green building consultation and ratings facilitation services to MAPAL India Private Limited for their head office, at Paduvampalli, Coimbatore. Mapal has scored 86 points out of the available 110 points making it India's Highest ranking Green Building (in this version as of May 2024) rated by GBCI.
The admin building is a net Zero Energy Building where 100% of its annual energy use is generated through a on-site solar power plant. It is also one of the most intelligent, automated and smartest buildings.
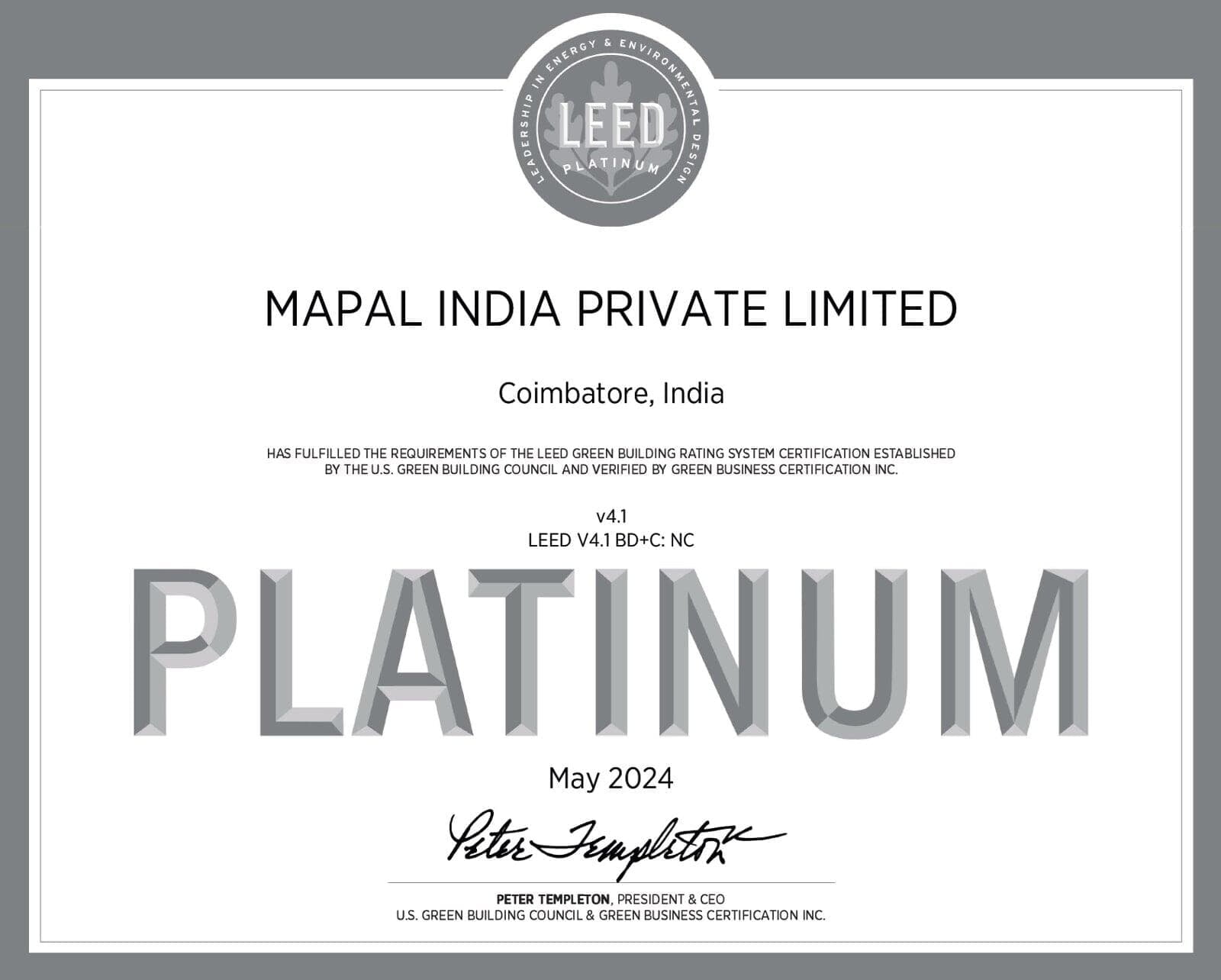
- The site has been developed in a designated industrial zone and not in a environmentally sensitive greenfield site.
- More than 10 basic amenities are available within a 800 mtr walking distance, reducing vehicle use.
- 200 mm of fertile top soil was stored near site and was reused for landscaping purposes.
- Bicycle parking along with shower and changing facilities to encourage cycling.
- Shuttle bus facility to nearest bus stops along with city pick up and drop, to reduce private vehicle use
- Provision for electric vehicle charging stations to encourage switch to electric vehicles
- Onsite parking to reduce disturbance on public roads.
- To protect and restore habitat over 50% of the site area is reserved for landscaping and planted with native species that promote biodiversity.
- Heat island effect is reduced by minimising paved surfaces, light coloured pavers and shaded car parks.
- Heat island effect from roof is reduced by using a cool roof and shading through solar panels
- Local biodiversity is further protected by reducing evening light pollution through provision of external blinds that shut light trespass to the outside and outdoor lighting is designed to ensure no excess light leaves the site boundary and no upward lighting is installed.
- All-electric hygienic kitchen to take care of staff and visitors’ breakfast and lunch requirements to reduce staff movements
The development achieves 84% potable water savings compared to NBC standards by installing water efficient plumbing fixtures.
Large quantities of water is saved in irrigation by using the treated wastewater and stored rainwater to meet 100% of the irrigation demand..
100% wastewater is treated to tertiary standards and will be used for landscaping & flushing purposes.
The site is a zero-discharge site with 100% of rainwater is stored and reused with the excess being recharged.
Highly efficient drip and sprinkler irrigation systems are installed to further minimise non-potable water use.
Domestic Water quality is regularly tested to ensure all BIS norms are met.
Ground water quantity and quality will be improved gradually through recharge wells to percolate all excess water into the ground.
High end automation ensures all tanks are level controlled with no human input required for water conveyance.
All water sources have digital sub metering linked with the BMS to monitor water use and identify wastages.
State of the art Sequencing Batch Reactor (SBR) based STP System, Raw water treatment using pressure sand filter & carbon filter, Rain water additional treatment using dual-media filters & UV treatment leading to high-quality water use improving efficiency by way of leak free working of al fixtures.
- 100% Net Zero Energy Building with the project having a 430 KW solar PV system installed on the roof which caters to all the energy loads in the admin building and has further helped reduce the campus's energy consumption by over 40%.
- Digital Energy meters have been installed in all major energy consuming areas including process loads and building loads.
- The building has achieved over 17% energy savings through the use of high performance building materials, HVAC, lighting and state of the art automation linked to the Building Management System.
- The envelope measures include use of high performance glass, external blinds along with AAC blocks and insulated roof assembly.
- The building generates close to 7 lakh units of power annually through its 430 KW rooftop solar PV system.
- All HVAC systems use eco-friendly refrigerants to reduce greenhouse gas emissions.
- The project has the most modern BMS that constantly measures the energy and water use at various sources and a plan is in place to correct any malfunction of the systems.
- A third party commissioning of equipment was organised to test all systems were working as per design and an operation and maintenance manual was also prepared to ensure efficient operations.
- Water and electricity meters to measure zone / purpose wise utilization and energy dashboards displaying solar power generation, savings and utilization data to improve sensitivity and awareness among building occupants. Display of energy saving targets and the achievement levels to improve outcome.
- High efficiency LED lighting with optimised design to achieve 6W/Sqm Lighting Power Density.
- The project already has sustainable purchasing practices in place. These have now been formalised through the purchasing policy which has been created using the LEED V4.1 framework.
- A dedicated team and a waste storage space are provided to store the collected waste before handing it over to the third-party recycler. The collected waste which are generated such as Paper, Plastic, Cartons will be sent to recycling on a weekly basis.
- All organic wastes are converted to manure and reused on site using a composting system
- Special provisions have been made through multiple bins on every floor for source segregation, Storage and collection of recyclable wastes.
- Over 39% of the construction wastes generated were recycled or reused, thereby diverting it from landfills.
- Over 12% of the total value of the civil construction materials comes from recycled materials.
- Over 9% of all civil materials were procured from within 400 km radius from site, thereby reducing transport impacts.
- A detailed Life Cycle Analysis was conducted to measure the impact of the building materials on global warming, acidification and eutrophication.
- The project is designed to ensure over 100% of the regularly occupied spaces have Fresh air ventilation as per the latest ASHRAE standards. The ventilation system pumps in 45% more treated fresh air compared to code requirements.
- Over 86% of the Building Occupants has Connectivity to the Exterior View.
- The entire campus is a no smoking campus.
- Periodic indoor air quality tests are done to keep a check on indoor environmental conditions and remedial measures are taken as per the pollutant identified.
- The factory has fully changed over to organic pest management and organic landscaping practices to minimise the use of harmful chemicals in the factory.
- All food served at the factory procured within 150 Kms radius to ensure freshness and minimise its transportation impact.
- The factory follows a robust green cleaning policy and has fully upgraded to using only natural and organic green cleaners.
- The building has 13 CO2 sensors in all densely occupied spaces that is linked to the Demand Control Ventilation. Additional fresh air is automatically pumped in when CO2 level go above 800 PPM or when the outside vs inside differential is beyond 500 PPM
- Best practices were followed during construction to reduce contamination of indoor environment.
- A building flush out was carried out and indoor air quality was tested before occupancy.
- Materials were carefully chosen to ensure only low emitting/low VOC paints, coating, adhesives and sealants were used. All composite wood used is free of added Urea Formaldehyde.
- The building uses entryway systems to reduce dust indoors from occupant footwear.
- The HVAC system uses high efficiency MERV 13 filters to filter particles even below 10 micron.
- Thermal comfort has been designed to meet international ASHRAE 55 standards to ensure health and productivity of occupants
- Over 41% of the regularly occupied spaces are daylit optimally through optimisation of glass. Daylight sensors are provided to ensure lights turn on or off based in the indoor light levels.
- All interior partitions are specially selected based on its acoustic rating to minimise indoor noise levels.
- 18,211 Sqm mini forest has been planted with over 1500 trees which sequesters 29,65,000 Kgs of CO2 over its lifetime.
- Relatively switch free office with most lighting and the air-cons controlled through touch panels and/or customized mobile application installed on each employee phones.
- 100% of the lighting is controlled using occupancy sensors operated based on LUX levels controlled by the BMS system ensuring maximum energy efficiency with provision to calibrate individually based on occupant’s individual needs
- Continuous air quality measurement for Volatile Organic Compounds (VOCs) using indoor air quality monitors.
- Need based operation of back-up diesel generator, when there is a power failure, the diesel generators are selectively switched on based on the demand.
- Automation of fault detection and generation of notifications and alarms using Siemens BMS system.
- Automated gates and access control office floors.
- Air-conditioning system monitoring, operation, fault detection and notification generation
- CCTV system monitoring & automatic fault detection and notification generation. Perimeter detection and raising of security alerts.
- Scheduling of streetlights, parking lights, gate lights, switching on of occupancy sensors based on lux levels
- Automation of fresh water, flushing water pumping and filtration system using water level indicators for completely automated operation.
- Automated operation of garden sprinkler system based on humidity and temperature logs and schedules
- Sewage Treatment Plant monitoring, logging, fault detection and notification generation.
- LT Panel monitoring, logging of critical parameters, fault detection and notification generation.
- Water filtration systems monitoring, logging, fault detection and notification generation